
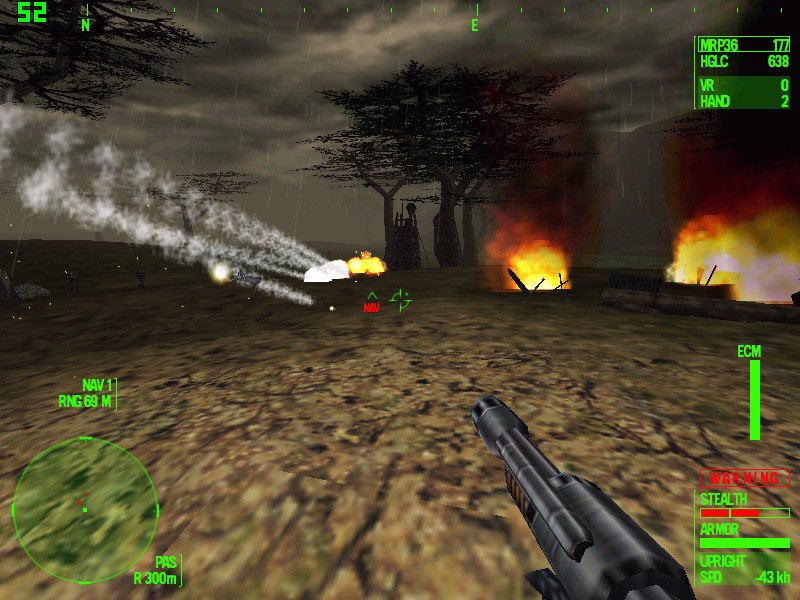
Remember that each stage adds some friction. Keep the gearing pared down to the essentials. ▪īuild your robot in a way that allows easy replacement of the gears, so you can experiment with different ratios in a time-efficient manner. You have to balance the two effects, and the optimal choice depends also on the length of the race: Favor acceleration on short tracks, and maximum top speed on longer ones. The problem is that a short gear also has low top speed. The shorter the gear, the shorter the time it takes to reach the maximum speed. The gear ratio and mass will have a strong influence on the acceleration rate of your vehicle here is a short list of tips: ▪ Even with these limits, there are still many variables to consider in your design process. Of course, the rules of the competition will probably specify the allowed motor type and a restriction on power source.įor the purposes of this chapter, it is assumed that the competition limits the vehicle to two NXT motors and an NXT as the power source. Also available are the traditional MINDSTORMS “gray” motors, as well as the black “RC Buggy” motors that are now available as a separate motor pack (LEGO set #8287) and as part of kits such as the yellow crane (LEGO set #8421). With the addition of the new NXT motors, three types of motors are widely available. Using electric motors, the maximum power you can apply to your race car depends on the kind and number of motors, and the current you supply them. The speed of a vehicle is affected by a number of factors: motor power, gear ratio, mass, and friction. But stay tuned, and take a closer look at the implications of this definition. “A starting line a finish line the fastest robot to cover the distance wins.” Described in these terms, the race sounds boring. In Building Robots with LEGO Mindstorms NXT, 2007 Drag Racing The AGMA power ratings based on wear and pitting resistance are presented in Section 11.3 and an associated design procedure in Section 11.4. Worm and wheel gear-sets tend to fail due to pitting and wear (see Dudley, 1984 Maitra, 1994 Radzevich, 2016). Such information is critical to enable suitable bearings to be selected for both shafts. see Dudás, 2005 Litvin and Kin, 1992) and this is outlined in Section 11.2. Cast iron and polymers are sometimes used for lightly loaded, low speed applications.Īn analysis of the forces associated a worm and wheel gear-set can be undertaken readily (e.g. Sand-cast or forged bronze is commonly used. The worm gear needs to be of softer material that is compliant enough to run-in and conform to the worm under the high sliding running conditions. They are typically ground or polished to a roughness of R a = 0.4 μm. The worm is subject to high stresses and is normally made using a hardened steel such as AISI 1020, 1117, 8620, 4320 hardened to HRC 58-62 or a medium carbon steel such as AISI 4140 or 4150 induction or flame hardened to a case of HRC 58-62 ( Norton, 2006). The tooth forms for worm and wheel gear sets are not involutes. The various terms are illustrated in Fig. 31.15. The fillet is the rounded portion at the bottom of the tooth space.
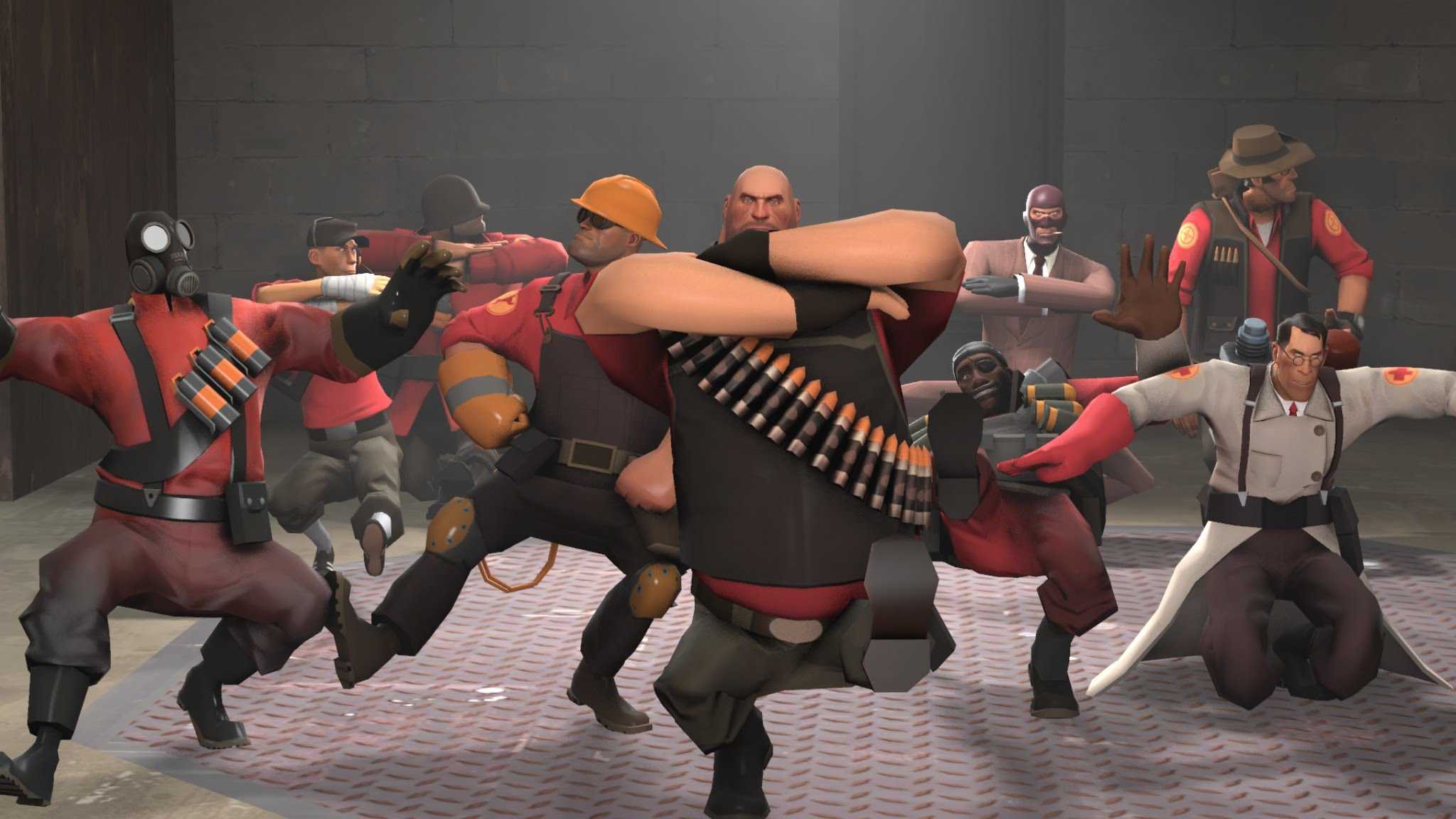
The pressure angle is the angle formed between the common tangent and the line of action. The line of action is the common tangent to the base circles, and the path of contact is that part of the line of action where contact takes place between the teeth. the number of teeth divided by the pitch-circle diameter. The diametral pitch is the reciprocal of the module, i.e. The module is the pitch-circle diameter divided by the number of teeth. The tooth width is the length of arc from one side of the tooth to the other, measured round the pitch-circle circumference. The circular pitch is the distance from a point on one tooth to the corresponding point on the next tooth, measured round the pitch-circle circumference. The whole depth of the tooth is the sum of the addendum and the dedendum. The clearance is the algebraic difference between the addendum and the dedendum. The dedendum is the radial depth of the tooth from the pitch circle to the root of the tooth. The addendum is the radial depth of the tooth from the pitch circle to the tooth tip. The center distance is the sum of the pitch-circle radii of the two gears in mesh. The root diameter is the diameter at the base of the tooth. The base circle is the circle from which the involute is generated. The pitch circles are imaginary friction discs, and they touch at the pitch point. The pitch-circle diameters of a pair of gears are the diameters of cylinders co-axial with the gears which will roll together without slip.
